APMotorsport Megane 3 Cup Project.
- Jahee Campbell-Brennan
- Apr 23, 2020
- 5 min read
Updated: May 11, 2020

Converted from a standard Renault Megane Sport 3 road chassis by APMotorsport (APM), this was built as a showcase and trackday/R&D car to a very high standard. Specifications are as follows:
Stripping of interior (all OEM seats, partial dash removal, removal of all interior trim)
Powertrain modifications; custom engine calibration, larger intercooler, cold air feed, less restrictive exhaust system (3” downpipe & DeCat)
FIA/MSA compliant Group N approved safety cage with fire suppression system
Race seats and safety harnesses
Polycarbonate side and rear windows
GRP doors & boot lid
AST 2-way adjustable dampers with custom spring rates
Endurance specification race brake pads
ATS GTR 17x 9J Racing wheels
Dunlop Direzza DZ03G H1 Tyres
AIM MXS Dash Display & Data Logger
Further to the general build of the car, Wavey Dynamics was working with APM in the capacity of aerodynamics and vehicle/chassis dynamics consultancy – This article is a short technical write-up of our involvement outlining the process and understanding applied.
Aerodynamics:
Given the restriction and practicality of implementing more aggressive aerodynamics to this road car platform, attention was mainly focused on opportunities for positive lift reduction rather than negative lift generation.
The first action was to provide venting to the wheel arches and provide a channel for high pressure air to evacuate. A front splitter was employed to aid in the ‘splitting’ of free stream flow above and below the car in an ordered fashion - given the rough and unshielded underfloor, the transition into turbulent and unordered flow post-splitter meant that no advantage from a rear diffuser would be seen. No rear wing was installed in order to preserve the aerodynamic balance; the presence of a small lip on the trailing edge of the roof as installed at factory was the only flow modifier here, its purpose to delay the establishment of low pressure air 'bubble' behind the car and therefore reduce drag force.
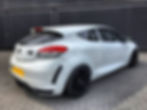
Chassis Dynamics
With the FIA spec cage increasing the torsional stiffness as well as stiffness in the warping mode by orders of magnitude versus the stock body, this modification provided a very strong platform from which the springs, anti-roll bars (ARBs) and dampers could react and manage the force and moment inputs from both the road surface and lateral accelerations.
Beginning with the tyres; The large increase in cornering stiffness (N of lateral force/° of slip angle) provided by these motorsport tyres compared to the road tyre, combined with freedom of adjustment of static and dynamic attributes allowed much greater freedom to influence the following parameters and maximise the performance of the car.
Lateral Forces front/rear
Yawing Moments
Understeer gradient
Characteristics of transitive periods before steady-state cornering equilibrium is reached.
The car was taken to the Nürburgring Nordschleife for tuning of the chassis dynamics accompanied by myself and the APM team.
Before adjustments were made, a baseline performance was recorded through quantitative (lap/sector times) and subjective (driver feedback) measurement. No further data streams were available during this test.
Once this was done, the first modification made was alignment/geometry of the wheels to a more track focused setting. The OEM control arms and uprights meant the kinematics of the wheels were fixed, however adjustments to static toe and camber values was possible via aftermarket camber plates at the top mounts and factory adjustable steering arms at the front axle, adjustment of camber and toe at the rear was achieved via shims. At request, values were set as - Front = -3.5° camber (max), toe undisclosed (proprietary) : Rear = -1.9° camber, rear toe not adjustable (no further rear camber/toe shims available), the intention was to increment values based on observations of the driver and tyre wear profile as testing progressed.
With further track time the feedback was positive. It was noted that the front tyres were not wearing evenly and there was a strip of contact area that was unused, indicating the initial camber values were slightly too aggressive, during this test there was no further opportunity to make adjustments here.
Focus was then turned to the adjustment of damping values with the aim of both reducing the variation in contact patch pressure that the tyre experienced on the track and controlling the balance of the car during transition to steady-state cornering — This AST system allowed individual rebound and compression damping adjustment; the initial factory settings of these dampers were very well judged, but it was noted that there was not enough rear rebound damping on certain high speed sections of the track. Adjustments were made to this, with positive result to the stability of the rear.

Further adjustments were made to the damping before the end of the test session and a notable lap time reduction was seen. Overall, a successful weekend of testing from which a strong foundation to further refine was attained.
The Megane chassis is very capable and with a little more time and focus it will be possible to maximise it’s potential, something both J C-B Engineering Consultants and APM are looking forward to.
Tyre Pressures
Often, little is discussed regarding the influence of tyre pressures in chassis dynamics discussion. With a variable such as tyre pressure fluctuating largely even from corner to corner as heat build up and rejection in the tyre causes the gas volume to expand and contract, it is hard to run a conclusive and thorough analysis of it’s influence to determine a ‘one-pressure-fits-all’ figure - however what can be done at a test such as this is a measurement of temperature distribution along the contact patch; the relationship between tyre temperature and contact patch shape is as follows:

Variation in tyre pressure between axles can occur due to intrinsic factors such as Centre of Gravity (CoG) placement, Centre of Aerodynamic Pressure (CoP) location, wheel geometry and drivetrain (FWD/RWD), but ultimately, the effect of operating outside of optimal pressure is a reduction in cornering stiffness - the balance of the car shifts to over/understeer during running; Surely confusing for un uninformed driver. The APM Megane in this case was monitored and set accordingly, with the rear axle at slightly lower pressure than front proving optimal - due to the forward weight bias.
Conclusions & Future improvements
This test was almost entirely based on subjective data; followings tests would necessitate quantitative measurements to provide the ability for real analysis and comparison of changes, however for the cars first laps following build completion, useful strides were made with the techniques outlined above.
It is my judgement that the spring rates selected on this occasion were slightly too stiff for the track in question. The Nürburgring Nordschleife is a relatively ‘bumpy’ track, with many high amplitude excursions of varying frequency – with springs too stiff the contact patch pressure variation was large, this was felt in a skittish character over medium speed, rough sections of track. I would therefore recommend that slightly softer springs would be useful and with current geometry would also have the benefit of further utilising the unused section of contact patch via increased body roll.
To reduce the transitive period from initial steering input to steady state equilibrium in the front axle (otherwise described as ‘turn in’) as requested by the driver – an option to explore would be to obtain some adjustment in the front ARB, this would have the benefit of leaving the heave response unchanged but would alter the proportion of lateral weight transfer between the front and rear axles. Care must be taken here not to upset the neutral steering response (Understeer Gradient = 0) That we have been focusing on achieving throughout this test.
With resources allowing, I would further recommend that we perform various ADAMS simulations of the vehicle to provide much needed quantitative data of the spring and damping rates and therefore allow us real in-depth optimisation. Further testing could then be used to correlate this, reducing testing expense and time.
Myself and my client welcome any contact and questions.